Understanding Dispensing Techniques: A Closer Look at Contact and Non-Contact Methods
11/5/20242 min read
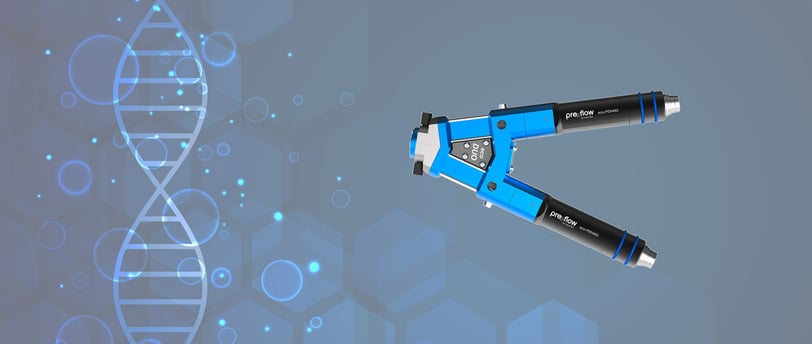
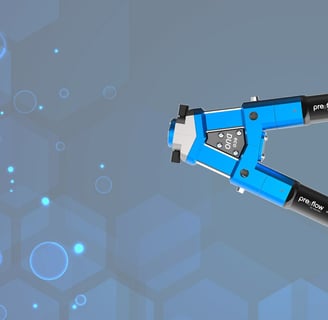
Introduction to Dispensing Techniques
Dispensing techniques are crucial in various industries, particularly when it comes to applying small amounts of liquids or adhesives. There are two primary methods of dispensing: classic contact dispensing and non-contact dispensing. Each of these methods has its specific applications and implications that can significantly affect the quality and efficiency of the dispensing process.
Classic Contact Dispensing Explained
Classic contact dispensing is a technique where the drop forms at the nozzle's exit and is then deposited by direct contact with the surface. This method is as old as the practice itself of dividing a medium, often held in larger containers, into smaller quantities for application. A classic example is applying adhesive from a tube; the adhesive is transferred to the part only when the nozzle tip touches it.
While contact dispensing is straightforward and widely used, it comes with several disadvantages. Firstly, dispensing can be slow, as the process requires precise alignment and steady hand control. Furthermore, direct contact means that the part being worked on has to be touched, which can lead to potential damage. For instance, delicate components may be scratched or deform due to the pressure applied during dispensing.
Another issue with contact dispensing is that it can sometimes lead to adhesive forming threads or strings, creating a messy application. Additionally, the application is not always ideal, as the dispensing material may not adhere evenly across the surface. These challenges can affect both the aesthetic and functional outcomes of the application, especially in high-precision environments.
The Advantages of Non-Contact Dispensing
In contrast, non-contact dispensing techniques have gained popularity due to their ability to avoid many of the pitfalls associated with contact methods. This method allows for the application of liquids without direct contact with the surface, typically using methods such as air pressure, ultrasonic waves, or controlled droplets. This mode of dispensing significantly reduces the risk of damaging sensitive parts.
Non-contact techniques enhance the speed of the dispensing process, making it suitable for high-throughput production lines. Furthermore, this method minimizes the chances of adhesive strings forming, leading to cleaner, more precise applications. The absence of contact also aids in maintaining the integrity of both the fluid being dispensed and the surfaces involved. As such, non-contact dispensing is often preferred in modern applications requiring precision and efficiency.
Conclusion
Understanding the various dispensing techniques available, including the classic contact and non-contact methods, is essential for optimizing any application process. While classic contact dispensing has its applications, the benefits of non-contact techniques often outweigh the limitations, especially in delicate, high-precision tasks. As technology advances, exploring innovative dispensing methods can lead to enhanced efficiency and effectiveness in liquid handling.
China
Liandong Yougu Garden, No.1 East Second District, Jiansha Road, Danzao Town, Nanhai District, Foshan City
TENSA TECHNOLOGY (Subsidiary of FST Dispensing pump)
Email : sales@tensatech.com
Singapore
12 Joo Koon Crescent #01 Singapore 629013
Tel : +86 13360343644
Whatsapp : +86 13360343644